Understanding Precision Die Casting in China
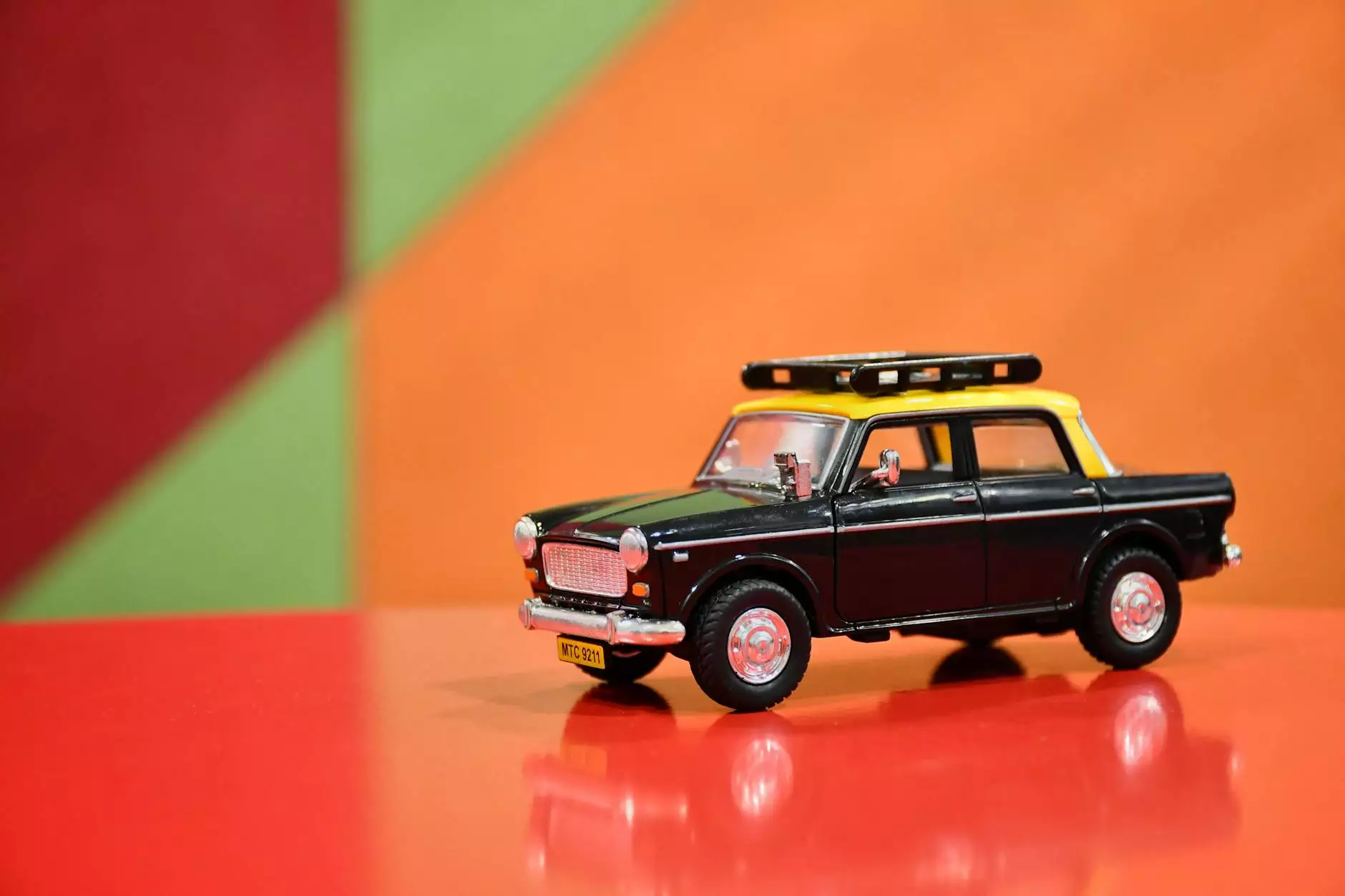
The landscape of manufacturing has transformed dramatically in recent years, with precision die casting in China emerging as a significant player in the global market. This method not only enhances production efficiency but also ensures high-quality standards that modern businesses demand.
What is Precision Die Casting?
Precision die casting is a manufacturing process that involves pouring molten metal into a mold to create intricate shapes with high dimensional accuracy. This technique is ideal for producing complex designs that require fine details and tight tolerances, making it an excellent choice for various industries, including automotive, aerospace, and electronics.
Key Benefits of Precision Die Casting
- High Precision and Accuracy: The process boasts tight tolerances, typically reaching up to ±0.1 mm, allowing parts to fit seamlessly in assemblies.
- Cost-Effectiveness: Although the initial mold costs can be high, the overall production costs decrease significantly with mass production.
- Versatility: Precision die casting accommodates a wide range of materials, including aluminum, zinc, and magnesium, catering to diverse industry requirements.
- High Surface Quality: Cast components often require minimal machining, saving time and reducing waste.
- Increased Strength: The casting process enhances the mechanical properties of metals, resulting in stronger components.
The Precision Die Casting Process
The process of precision die casting can be broken down into several key steps. Understanding these steps allows businesses to appreciate the intricacies involved in producing high-quality components.
1. Design and Prototype
The journey begins with the design phase. Advanced Computer-Aided Design (CAD) software is used to create detailed models of the parts to be manufactured. A prototype is then developed using 3D printing or traditional methods to evaluate the design and make adjustments as necessary.
2. Mold Creation
The next phase involves creating a mold, which is usually made from steel or iron. This mold is designed to withstand high pressure and heat, ensuring durability over many production cycles. Precision in mold design is critical as it directly affects the final product’s quality.
3. Melting and Pouring
Once the mold is ready, the chosen metal is heated until it reaches a molten state. The liquid metal is then poured into the mold at high pressure, ensuring it fills every cavity and detail accurately.
4. Cooling and Solidifying
After the molten metal fills the mold, it is allowed to cool and solidify. This cooling phase is crucial as it determines the mechanical properties of the final product. Advanced cooling techniques can be implemented to accelerate this process.
5. Ejection and Finishing
After the metal has completely cooled and solidified, the die opens, and the finished part is ejected. This stage may also involve additional finishing processes, such as machining, polishing, or coating, to enhance the product's functionality and appearance.
Precision Die Casting in China: The Hub of Manufacturing
China has rapidly become the epicenter for precision die casting, attracting businesses globally looking for high-quality manufacturing solutions. Several factors contribute to this explosive growth:
1. Advanced Technology
Chinese manufacturers are at the forefront of adopting advanced die casting technologies. Automated systems and robotics help streamline production, ensuring higher efficiency and reduced labor costs.
2. Competitive Pricing
The abundance of skilled labor and lower overhead costs allows Chinese companies to offer highly competitive prices without compromising on quality. This is particularly beneficial for businesses seeking bulk production runs.
3. Rapid Turnaround Time
With well-established supply chains and logistics networks, manufacturers in China can deliver products faster than many competitors worldwide. This capability helps businesses reduce their time-to-market and meet consumer demand promptly.
4. Robust Infrastructure
China's infrastructure supports efficient manufacturing operations. Access to transportation networks, energy sources, and resources allows for the smooth movement of materials and finished products.
Choosing the Right Partner for Precision Die Casting
When considering precision die casting in China, selecting the right manufacturing partner is crucial. Here are some factors to consider:
1. Experience and Expertise
Look for manufacturers with extensive experience in precision die casting. Their knowledge of the process, materials, and quality controls will ensure a better end-product.
2. Quality Certifications
Check if the manufacturer holds relevant quality certifications, such as ISO 9001. This indicates a commitment to maintaining high-quality standards throughout their operations.
3. Technical Support
A good partner should offer technical support during the design and production phases. This includes assistance with design optimization and problem-solving during manufacturing.
4. Customer Reviews and Case Studies
Research reviews and case studies from previous clients. This information can provide valuable insights into the manufacturer’s reliability and product quality.
Applications of Precision Die Casting
Precision die casting has wide-ranging applications across various industries. Let’s explore some of the main sectors benefiting from this process:
1. Automotive Industry
In the automotive sector, precision die casting is used to produce engine blocks, transmission housings, and other critical components that require high strength and lightweight properties.
2. Aerospace Sector
Components for aircraft, such as brackets, housings, and fittings, often utilize precision die casting. The aerospace industry's stringent regulations necessitate the precision and reliability offered by this manufacturing method.
3. Electronics and Electrical Appliances
Manufacturers in the electronics industry rely on precision die casting for producing casings, heat sinks, and connectors that demand precision and durability.
4. Consumer Products
From kitchen gadgets to furniture hardware, many consumer products utilize precision die casting to achieve desirable aesthetics and functionality that meets consumer expectations.
The Future of Precision Die Casting in China
The future of precision die casting in China looks promising, with advancements in technology and increasing demand across various sectors. Here are some trends to watch:
1. Automation and Robotics
The integration of automation and robotics will continue to revolutionize the precision die casting industry, enhancing production capabilities and reducing costs.
2. Eco-Friendly Practices
As sustainability becomes increasingly important, manufacturers are adopting greener practices, such as recycling materials and reducing waste during production.
3. Customization and Small Batch Production
More companies will embrace flexibility in production, offering customized designs and small batch runs to meet the changing demands of the market.
4. Digitalization of Processes
The use of digital technologies, such as IoT and big data analytics, will optimize production processes, improve quality control, and enable predictive maintenance approaches.
Conclusion
In conclusion, precision die casting in China presents a wealth of opportunities for businesses seeking high-quality manufacturing solutions. With its cost-effectiveness, precision, and versatility across various industries, it has solidified its role as a fundamental process in modern manufacturing. Partnering with the right manufacturer in China can unlock significant advantages, enabling companies to excel in their respective markets.
As industries continue to evolve, staying informed about advancements in precision die casting will be crucial for businesses looking to maintain a competitive edge.
precision die casting china